7 Ways to High ROI with Industrial Vending: #2 Increase the Use of Reconditioned Items
- Feb 1, 2020
- 2 min read
Everyone wants the newest item, so it is no surprise that employees prefer new items over reconditioned items. Using reconditioned, reground or re-sharpened items can result in significant savings when compared to the cost of new tools. New tools can easily cost five times more than an equivalent reground or reconditioned item.
Reconditioned items can include cutting tools, blades that need sharpening after a set number of uses, masks that need cleaning and recertification for safety every month, or gloves that need cleaning or any item that need periodic repair or maintenance.
Industrial vending machines uses a unique system that:
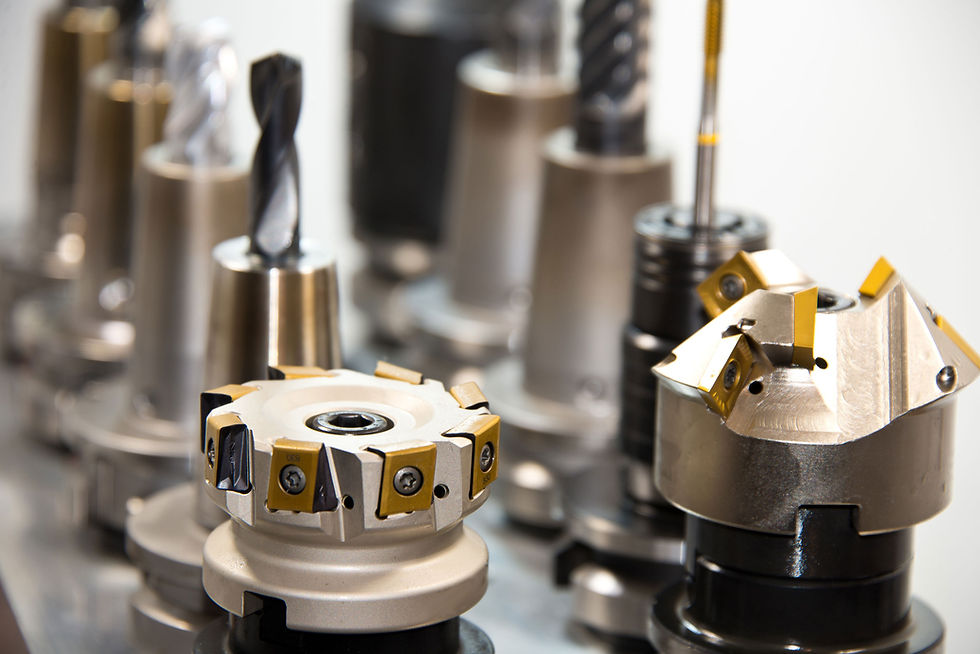
Issues regrinds and reconditioned items first, before allowing access to new items.
Allows managers to control access to regulate which items need to be issued for a specific job.
Gives supervisors the ability to check out new items if an operator needs it for a job.
Automatically tracks scrapped items and the number of times each tool is returned and reused.
Reports spikes and excesses, so that you can identify potential problems or maintenance issues that may go undetected by line operators.
This inventory management system has been so successful that some companies justify the entire cost of an industrial vending system solely from savings generated by pushing
reconditioned items. When you force the use of regrinds or reconditioned items, it’s common to get an 80% reduction in tool costs. Track items that need recalibration, cleaning, repair or lubrication after a number of uses and ensure that reconditioned items get used before new items. Forcing the use of reconditioned items can save you big money that would have been lost buying brand new replacement items.
Remember, this is only part two of a seven-part blog series on solutions that increase savings, efficiency, and productivity.
Click here to go back to the first blog of this series about reducing consumption. Stay tuned for the next post about reductions in obsolete inventory.
Great insights! Increasing the use of reconditioned items is a smart and sustainable way to boost ROI. This article offers practical tips for businesses looking to optimize industrial vending strategies. chicago vending services
It's a great way to maximize resource use while reducing waste. Alongside this, ensuring optimal working conditions is key. Something I’ve found helpful in creating a more productive environment is ensuring good air quality, especially in industrial settings. https://sensibo.com/ offers smart solutions to help manage indoor air, improving comfort and efficiency. It’s a simple but effective way to create an environment where both people and machines can thrive. Definitely something worth considering alongside other cost-saving measures!